LM Wind Power launches fully recyclable thermoplastic wind turbine blade
Energy Disrupter
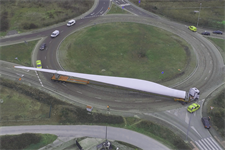
GE-owned LM Wind Power has completed the first prototype of a 100% recyclable wind turbine blade produced under its zero waste blade research (Zebra) consortium.
Blade manufacturer LM Wind Power designed and built the 62-metre blade, the world’s largest thermoplastic blade, at its Ponferrada plant in Spain. This milestone was achieved after a year of material development and testing.
Launched in September 2020 and led by French research centre IRT Jules Verne, the Zebra project brings together industrial companies including Arkema, polymer company Canoe, French utility Engie, LM Wind Power, Owens Corning and environmental services firm Suez to demonstrate the technical, economic and environmental benefits of thermoplastic wind turbine blades through a design approach that facilitates recycling.
The blade was made using French chemicals company Arkema’s Elium resin, which is a liquid thermoplastic resin known for its recyclable properties, and high-performance glass fabrics from composites producer Owens Corning. The resulting composite material is said to deliver similar performances to thermoset resins but with the key benefit of recyclability.
Elium-based composite components can be recycled using an advanced method called chemical recycling, which allows to fully de-polymerise the resin, separate the fibre from the resin, and recover new virgin resin and glass ready for reuse.
In addition to material testing and process trials, the companies have also made progress on optimising the manufacturing process by using automation, to reduce energy consumption and waste from production.
“With this project we are addressing two crucial industry challenges,” said John Korsgaard, senior director of engineering excellence at LM Wind Power.
“On one hand, we are progressing on our zero waste blade vision by preventing and recycling manufacturing waste. On the other, we are taking blade recyclability to a new level: the end-of-life thermoplastic composite blade material has high value in itself and can be readily utilised in other industries as material compounds but can also be depolymerised and the resin reused in the production of new blades.”
LM Wind Power will now start full-scale structural lifetime testing at its test and validation centre in Denmark, to verify the performance of the composite material and its suitability for future sustainable blade production. Finally, end-of-life recycling methods will also be validated. The project is scheduled to end in 2023.