Innovative drilling tech at the forefront of Finland geothermal project
Energy Disrupter
The GM2000 drilling rig by Geomachine and developed with QHeat is an innovative drilling rig integrating automation and IoT technologies.
A few weeks ago, a geothermal project at the site of waste incineration plant by Lounavoima set a new record with the drilling of a thermal well to a depth of 2008 meters. Drilling to this depth allows for much greater thermal output and thermal storage capacity for the waste incineration plant.
The developer behind the geothermal project is the technology company QHeat, which had also been involved in a geothermal district heating project in Vantaa, Finland earlier this year. Another crucial component in the execution of the Lounavoima project is the GM2000 drilling technology by Geomachine.
An integrated drilling solution
The GM2000 well drilling technology is not just a drilling rig, but a complete geothermal drilling solution that includes a compressed air system and an intelligent control and recording system for optimizing the drilling process.
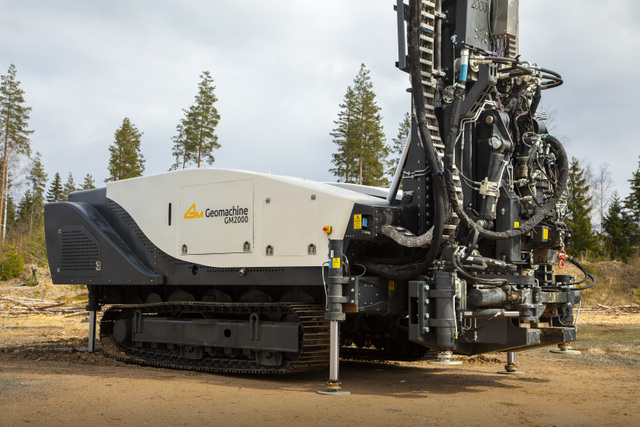
“When we started looking for a practical implementer for our innovation a few years ago, we realized that there was no expertise in deep geothermal well drilling in Finland. Geomachine has decades of experience in ground investigation and down-the-hole hammer drilling, so we engaged in discussions about refining our concept with them. It became clear that they had the expertise needed to develop the drilling rig,” said Erika Salmenvaara, CEO of QHeat.
In designing the GM2000 well drilling rig, special attention has been given to overall cost-effectiveness, automatic data recording, real-time analysis of the drilling process, and work safety. “The adoption of the GM2000 solution has brought various benefits. Drillers’ job satisfaction has improved because they now have a modern tool at their disposal. Work is safer, and drillers are no longer exposed to emissions as the rig can be controlled remotely. Due to the rig’s data-driven control, the driller knows what is happening in the hole at all times. Overall, work has become safer and of higher quality.”
Easy mobilization and fast deployment are some of the other key features of GM2000. It is small in size, easy to transport, and fast to prepare for drilling.
From driller to process operator
Automation is an important part of the design process of the GM2000. Through a CAN-bus control system, automated drilling can be done with GM Weight-on-Bit (WoB) control. This keeps the drill bit pressure at pre-defined target levels, thus optimizing the drilling speed while minimizing wear and damage on the bit.
The tilting rotary head is automated to work together with the feeding table for the loading and unloading of the drill string. Opening and tightening of the rod connections are made easy with a hydraulic clamp and sliding rod holder. All operations are protected by a safety radar system. All this makes drilling safe, fast, and easy for the operator.
Using the GMTrackerDTH data-logging software, well drilling data collected, monitored in real-time, analyzed, and reported. The drilling progress can be recorded and tracked graphically. The values monitored include drilling feed speed, rotation speed and torque, feed force, and drill bit pressure. When using a Geomachine compressor, the data-logger can also monitor the compressor’s fuel consumption, drilling pressure and air volume. The operator can also add notes to the drilling progress chart.
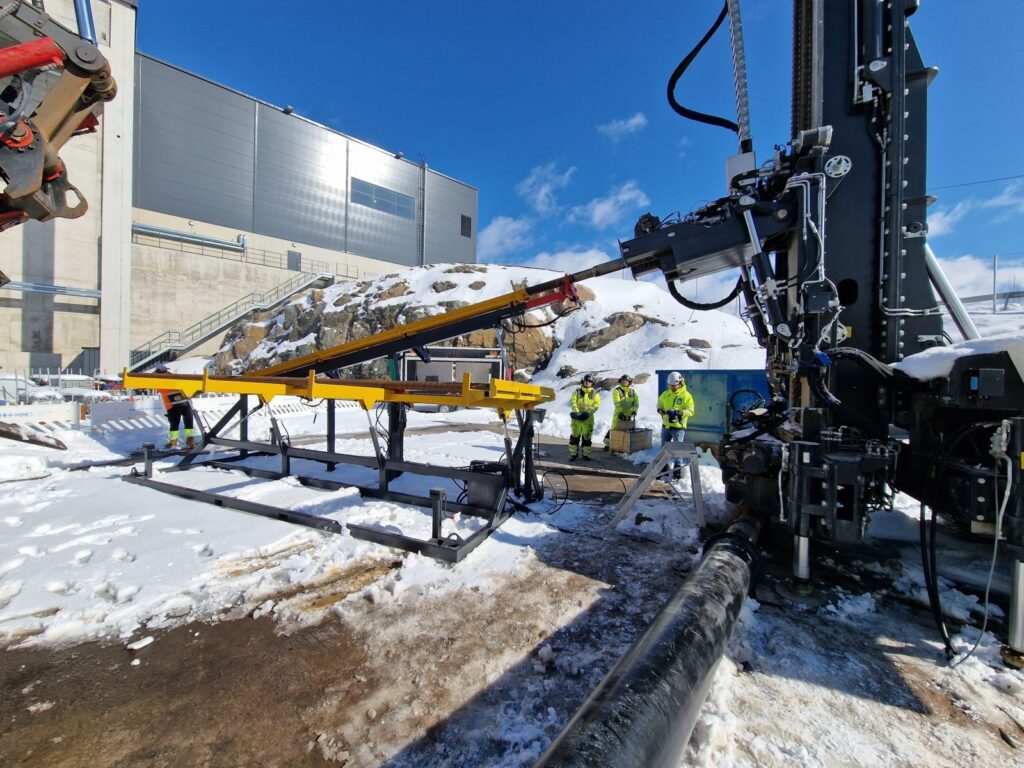
Machine learning is one of the superior features of the GMTrackerDTH. The operator can choose the monitored indicators, after which the software suggests adjustments based on what it learns during drilling.
GMTrackerDTH allows data analysis over multiple drilling sites and equipment choices to find the most economical values for the drilling process and enable predictability. The data-logger automatically measures soil composition and records rock socket connections and rock fractures, so it can also be used as a reporting tool.
All this helps to ensure a successful drilling process even in challenging conditions. The role of the machine operator changes from a driller to a process controller.
Collaboration leads to remarkable feats
According to Erika Salmenvaara, the collaboration with Geomachine is an excellent example of how combining forces can lead to an excellent outcome. “Our mission is to assist our customers on their carbon neutrality journey, particularly in heating. Our product is clean heating energy. Geomachine, on the other hand, offers the solution for practically implementing our mission. Even though we operate in different industries, we have found true synergy in achieving a common good.”
Both QHeat and Geomachine benefit from this collaboration in growing their respective businesses. “For us, collaboration enables us to sell our innovation as a tangible product to those who need it. Geomachine, on the other hand, adds a new solution to their product portfolio, expanding their offerings from ground investigation to geothermal energy drilling.”
In the future, the Geomachine drilling solution will be marketed to real estate investors, district heating developers, construction companies, and large property owners. There are also plans to augment the GM2000 with a provision for connection to an electric powerline. Geomachine’s mission is to contribute to taking the geothermal well drilling industry to a new and more productive era.
Source: Geomachine