Solution for controlled blade installation
Energy Disrupter
Wind Energy – Blade Installation
Huisman and Siemens Gamesa have combined their engineering and operational expertise in the development of a solution to stabilise wind turbine components during installation, especially blades, but also nacelles and tower segments.
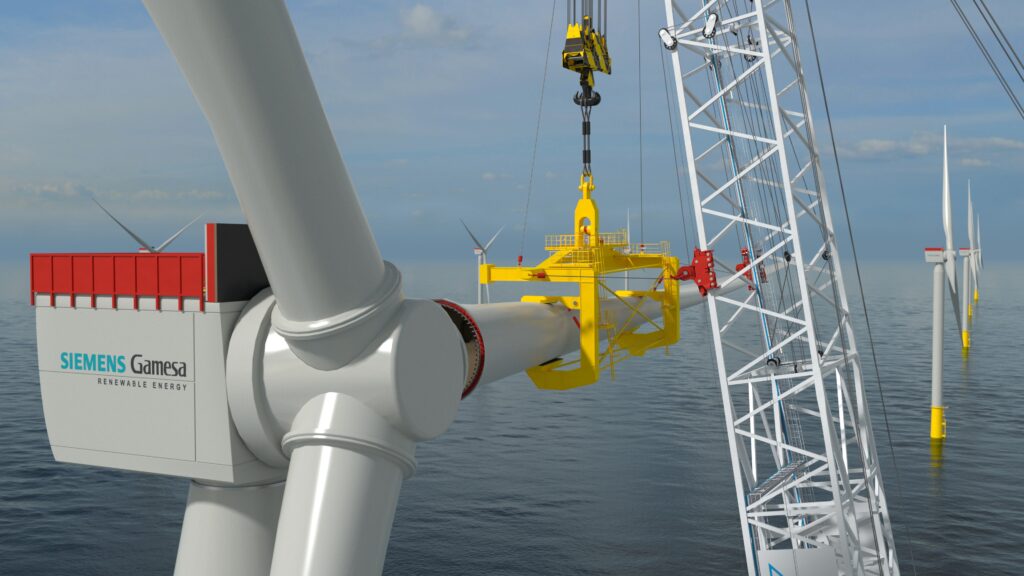
Controlling the movements of the relatively light blades of a turbine when suspended from a crane, has proven to be an installation challenge due to wind load. To mitigate operational downtime and increase the integrity of the delicate wind turbine components, Huisman and Siemens Gamesa developed the Travelling Load Stabilising System, for universal application in heavy lifting cranes.
The system consists of a combination of two pairs of tuggers working in unison to control to position of the load. One pair is fitted on independent trolleys that can travel along an integrated rail along the crane’s stiff boom. The trolleys automatically follow the main block to maintain an optimal tugger line configuration. The second pair of tugger lines is deployed from the crane tip providing a force perpendicular to the first pair of tuggers.
By approaching the load from two different directions, the system provides significantly more control than a conventional single pair of tuggers.
A specially designed control system holds the actual position of the load, resulting in a much stiffer restraint, and therefore a higher position accuracy compared to conventional tugger systems that rely on constant tension. In case of an unexpected overload, the system will give way but will return to its position setpoint when the force drops below the threshold again.
The Travelling Load Stabilising System functions as an integral part of the crane and could, therefore, be operated from the crane’s cabin as well from an optional walk around box (WAB).
Original Source: https://ocean-energyresources.com/2023/04/20/solution-for-controlled-blade-installation/