Wind turbine prices ‘could rise by up to 10%’ – Wood Mackenzie report
Energy Disrupter
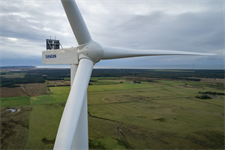
Increases in commodity prices, logistics costs and coronavirus-related challenges could push wind turbine prices up to as much as 10% over the next 12-18 months, according to new analysis from Wood Mackenzie.
A rise in steel, copper, aluminium and fibre prices, coupled with a four-fold increase in logistics costs, have increased turbine prices over the last six months, notes a recent Wood Mackenzie report. Consultants at the firm expect this trend to continue for the next four to five quarters.
“Turbine OEMs and component suppliers face a double whammy of cost increases and demand softening over the coming two years due to the US PTC [Production Tax Credit] and China feed-in-tariff phase-outs,” said Shashi Barla, Wood Mackenzie principal analyst. “Despite this rise in costs, we expect turbine prices to return to normal levels by the end of 2022.”
Challenges with supply chain constraints, pandemic-related restrictions in key markets, and cost inflation have affected the financial results announced by major OEMs in recent weeks, including Vestas and Siemens Gamesa.
Turbine manufacturers are also facing cost pressures from the ongoing US-China trade war, and are exploring the possibility of using India as an export hub from where to supply the Asia Pacific market, according to Wood Mackenzie
Because demand increases for the Indian market have failed to materialise, OEMs and suppliers have been able “to leverage excess production capacity to serve export markets cost-effectively”, said Barla. “As OEMs continue to manufacture the latest generation turbines in India, component suppliers are expanding within the market to produce components closer to their clients’ nacelle factories.”
The availability of critical capital components and raw materials could endanger country-level decarbonisation targets, Barla warned. “Offshore nacelle capacity, carbon fibres, pultrusions, permanent magnet generators, large-diameter main shaft bearings, gearbox bearings, semiconductors and specialised castings are at risk of future shortages.”
The emergence of bottlenecks for important materials over the next four or five years will force OEMs and their suppliers to “adopt next-generation technologies and materials”, he said.