Dogger Bank to trial high-energy rapid welding method
Energy Disrupter
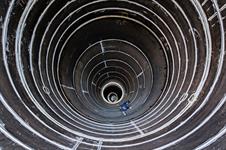
A large-scale pilot of a new process to significantly reduce welding times is due to be debuted at the first 1.2GW phase of the Dogger Bank offshore wind complex.
Ebflow reduced pressure electron beam (RPEB) welding will be used for the project’s monopile foundations.
RPEB uses heat generated by a beam of high-energy electrons to make a high strength and durable welded steel join.
It has been developed as part of the Rapidweld project, which consists of energy company SSE Renewables, manufacturer of the technology Cambridge Vacuum Engineering, offshore foundations manufacturer Sif, and welding research establishment TWI.
Through the Rapidweld project, the partners aim to create an industry-approved welding process for offshore wind that is more productive and sustainable than established methods, while reducing energy and material costs.
They believe RPEB will reduce welding time by 95%, be 94% more energy efficient, and deliver a 98% overall cost reduction compared to traditional submerged arc welding.
Dogger Bank A is the first phase of the 3.6GW Dogger Bank offshore wind complex off the north-east coast of England. It is due to be the largest wind farm in the world.
SSE (40%), Equinor and Eni (20%) own the first two 1.2GW phases, while SSE and Equinor each own a 50% stake in the third phase.