‘Melting’ blades offer glimpse of recyclable future
Energy Disrupter
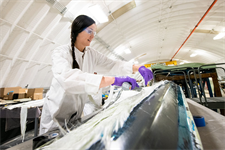
A 13-metre-long thermoplastic composite blade manufactured from a new material has had its structural integrity validated, NREL has confirmed.
NREL Researchers say the material could transform the wind industry, enhance renewable energy’s sustainability credentials and lower costs.
The feasibility of thermoplastic resin was first tested with a nine-metre blade, which was developed by Arkema in Pennsylvania and manufactured at NREL in Denver.
A thermoplastic composite blade was based on the same structural design as an epoxy blade – commonly woven with fibreglass – but was instead made from a two-part reactive acrylic-based resin called Elium.
Thermoplastic resin also allows for longer, lighter and cheaper blades. Until now, those made from thermoset resin were more energy and labour-intensive manufacture and decommissioned blades have often gone to landfill.
Derek Berry, co-author of a new paper, Structural Comparison of a Thermoplastic Composite Wind Turbine Blade and a Thermoset Composite Wind Turbine Blade, and a NREL senior engineer said: “With thermoset resin systems, it’s almost like when you fry an egg. You can’t reverse that.
“But with a thermoplastic resin system, you can make a blade out of it. You heat it to a certain temperature, and it melts back down. You can get the liquid resin back and reuse that.”
Further, the thermoplastic resin cures at room temperature, reducing the labour requirement, which accounts for about 40% of the cost of a blade.
NREL is home to the Composites Manufacturing Education and Technology (CoMET) Facility at the Flatirons Campus near Boulder, Colorado. Researchers design, manufacture and test composite blades there.
Working with Arkema and other Institute for Advanced Composites Manufacturing Innovation partners, they have demonstrated the advantages over thermoset resins.
Robynne Murray, NREL researcher, said: “The thermoplastic material absorbs more energy from loads on the blades due to the wind, which can reduce the wear and tear from these loads to the rest of the turbine system, which is a good thing.”
The resin could also allow manufacturers to build blades on-site, negating the need to transport them from a manufacturing facility.