Blade repair robot performs offshore wind’s ‘moon walk’
Energy Disrupter
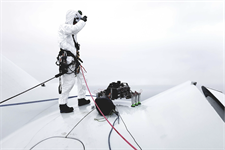
Researchers have celebrated offshore wind’s “moon walk” as a robot carried out a blade-walk on an offshore wind turbine for the first time.
Technology developer BladeBUG’s six-legged inspect-and-repair robot repeatedly scaled a vertically positioned blade on researcher body ORE Catapult’s 7MW Levenmouth Demonstration Turbine (formerly Samsung’s Fife demo) Levenmouth Demonstration Turbine (formerly Samsung’s Fife demo) (7MW) OffshoreMethil, Fife, Central Scotland, UK, Europe Click to see full details in tests last month.
Researchers explained that the blade walk demonstrates the BladeBUG robot’s real-word capabilities and suggested that robot inspection of turbine blades could increase safety and reduce costs.
The BladeBUG robot is a robotic system that can remotely inspect and repair critical infrastructure, including wind turbines. Its developer – a company of the same name – aims to use the robot to inspect blade surfaces for emergent cracks and imperfections, transmit data on their condition back to shore and resurface the blades
It had previously been tested in a controlled environment at ORE Catapult’s National Renewable Energy Centre in Blyth, north-east England, but had yet to be tested in the real world.
In walking 50 metres on a vertically positioned blade on the Levenmouth turbine off Fife, east Scotland, ORE Catapult researchers explained that BladeBuig had demonstrated:
- The perfect adherence of its vacuum-padded feet to blade surfaces in offshore conditions;
- Its ability to navigate the varying curvature of blade surfaces in a variety of scenarios;
- And its ability to transmit data from blade scans and live video-feed to technicians.
Chris Hill, ORE Catapult’s operational performance director, said: “It has a clear potential for cutting costs, reducing human offshore deployment and increasing blade lifetimes. But, we had yet to see how the robot would perform on a real turbine out at sea.
“I consider BladeBUG’s first walk at Levenmouth as offshore wind’s ‘moon walk’ – a historic milestone in the industry’s evolution. Robotics are here to stay, and they will be an essential ingredient to operating ever-expanding wind farms, deeper-water sites and faster, bigger turbines in the coming years.”
BladeBUG predicts its robotic system could reduce current costs of blade inspection techniques by 30% while ORE Catapult believes this figure could be as high as 50% for next-generation offshore wind turbines. Inspections are currently carried out by rope-access technicians.
Inspection costs have traditionally been an area of concern for offshore wind operators as sea conditions and faster tip speeds can lead to significant blade damage over time.
The BladeBUG tests are part of ORE Catapult’s multi-platform inspection, maintenance and repair in extreme environments project (Mimree) research project. Researches hope the project will demonstrate a fully autonomous inspection and repair mission to an offshore wind farm. Final trials are set to take place in mid-2021.